‘Onze klanten in de voedings- en verzorgingsindustrie en in de chemiesector produceren steeds vaker kleine batches en wisselen daardoor frequenter van product. Zo werken we momenteel aan een project waarbij elke 30 minuten een vul- en verpakkingslijn moet worden omgeschakeld naar een nieuw product’, zegt Andreas Seitz, Project Engineering Director Food & Chemical Solutions bij Optima consumer GmbH. ‘Tot voor kort draaiden we nog batches van één of twee weken. Nu is een half uur al heel normaal.’
'Vooral middelgrote bedrijven creëren deze trend in de bovengenoemde bedrijfstakken. Zo leveren we bijvoorbeeld aan een Duitse fabrikant die een uitgebreid assortiment produceert voor discounters en drogisterijen. Met producten variërend van vlekverwijderaars tot poetsmiddelen voor leer, hout en het interieur van auto's.'
Frequente productwisselingen - korte insteltijden
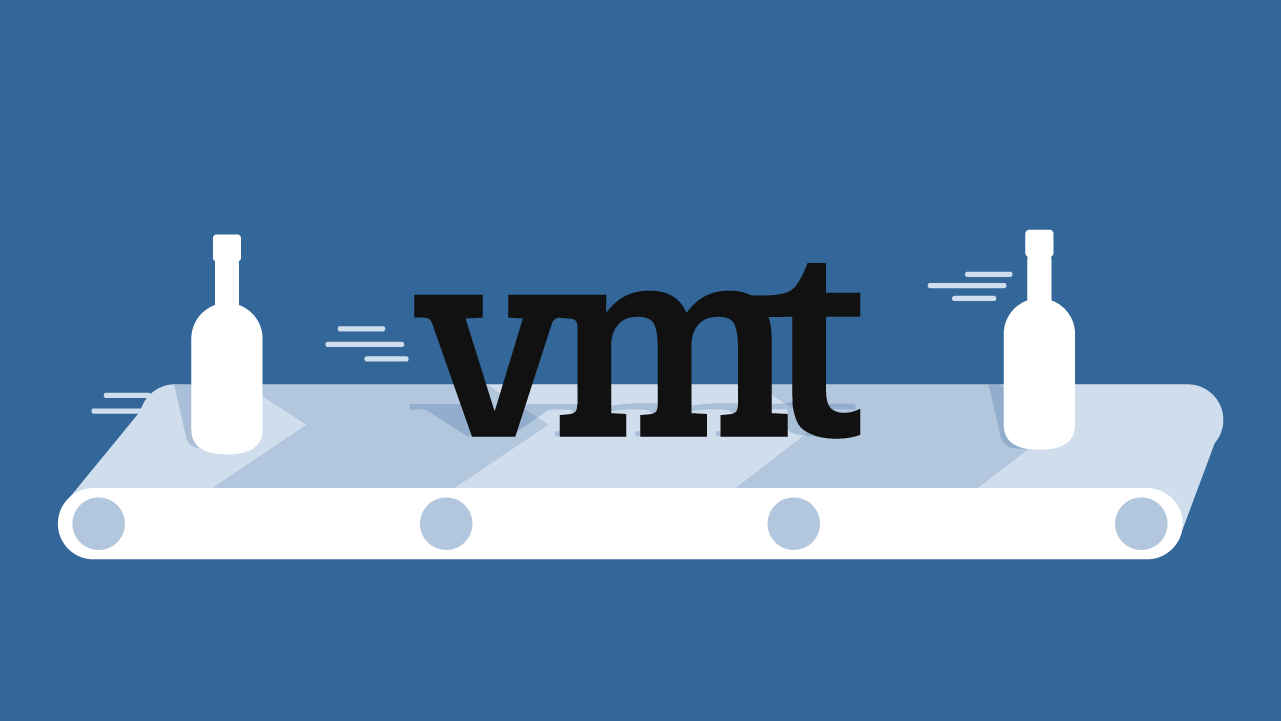
‘Dit zijn geen batches van een miljoen stuks, zoals we zien bij wasmiddelen’, legt Andreas Seitz uit. ‘Integendeel. Het zijn steeds vaker een paar duizend units uit een enorme variëteit aan producten, met een duizelingwekkende verscheidenheid aan verpakkingen wat betreft soorten, vormen en maten. Alleen al om logistieke redenen is ordergestuurde productie hier feitelijk onmisbaar.’
Bedrijven in deze ketens stellen navenant hoge eisen aan flexibiliteit, insteltijden en procesbetrouwbaarheid van de vul- en verpakkingslijnen. Optima heeft deze trend vroeg onderkend en levert verpakkingssystemen die zijn aangepast aan de veranderende marktomstandigheden. Volledige modularisatie en intensief gebruik van servotechnologie vormen hierbij het uitgangspunt.
In 2016 stapte het bedrijf voor hun sluitunits in verpakkingssystemen over op direct-drive technologie voor medium- en high-performance toepassingen. Hun draaitafels met maximaal 16 verticale sluitspindels worden aangedreven door PR01 lineaire-roterende motoren van LinMot.
Lineaire-roterende motoren voor flexibele productieprocessen
De snelle en krachtige elektromotoren, speciaal ontworpen voor sluit- en schroefprocessen, combineren individueel aanstuurbare, direct aangedreven lineaire en roterende motoren in één compacte behuizing met IP 64-bescherming.

‘Deze aandrijvingen voorzien niet alleen in snelle schroefprocessen met momenteel maximaal 600 sluitbewerkingen per minuut, maar stellen onze gebruikers bovendien in staat om kritische parameters zoals slaglengte, slagkracht, draaihoek en rotatiekoppel aan te passen via de gebruikersinterface op de verpakkingsmachine zelf’, zegt Andreas Seitz over de grote voordelen van deze nieuwe sluittechnologie.
‘Het tijdrovende wisselen van nokkenschijven en het handmatig instellen van slipkoppelingen is niet langer nodig, en dat maakt de insteltijden veel korter dan bij conventionele systemen.’
Efficiënte en duurzame directe aandrijvingen

Het onderhoud is bovendien gemakkelijker, omdat de lineaire en roterende bewegingen worden uitgevoerd met direct aangedreven lineaire en roterende aandrijvingen, die geen vuil of stof produceren en er evenmin gevoelig voor zijn. Bij storingen kan de betreffende spindel individueel worden uitgeschakeld totdat reparatie mogelijk is, terwijl ondertussen de productie in een lager tempo doordraait.
Bij geplande machinestops is het sluitsysteem leeg te draaien zonder productieverlies. Dit alles, in combinatie met het feit dat de geselecteerde parameters - zelfs na lange perioden van stilstand - direct worden gerealiseerd bij hervatting van de productie, draagt bij aan een hoge efficiëntie.
Compacte vormfactor en uitgebreide aansluitmogelijkheden
‘Het gebruik van lineaire-roterende motoren voor sluitprocessen is een logische stap naarmate de batchgroottes afnemen’, zegt ingenieur Markus Dierolf die als ontwerper bij Optima een grote bijdrage leverde aan het ontwerp van het nieuwe sluitsysteem. ‘We hebben gekozen voor LinMot omdat we hun producten al sinds 2011 gebruiken voor hanteringstoepassingen en er altijd goede ervaringen mee hebben gehad. Voor dit sluitsysteem was het vooral belangrijk dat de motoren zeer compact zijn en dat de servomotoren over allerlei aansluitmogelijkheden beschikken voor verschillende besturingssystemen.’
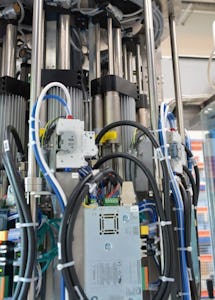
Zelfs als het nodig wordt om het formaat te veranderen, biedt de gebruikte servotechnologie, het ontbreken van nokschijven en de daaruit resulterende mechanische ontkoppeling talrijke voordelen. Alle spindels kunnen tegelijkertijd in de bovenste positie worden gezet om de toegankelijkheid te verbeteren tijdens het wisselen van de transportdelen en de sluitkoppen voor de aanpassing aan verschillende geometrieën. Een 'magnetische veer' houdt ze veilig in deze positie, zelfs wanneer de machine spanningsloos is.
LinMot ontwikkelde en produceert deze technologie onder de naam MagSpring. In tegenstelling tot mechanische veren levert deze techniek een constante kracht over het gehele werkbereik, wat optimaal is om de zwaartekracht te compenseren. Het werkingsprincipe is gebaseerd op de aantrekkingskracht van permanente magneten, dus is er geen energiebron nodig en kan de MagSpring probleemloos worden ingezet voor veiligheidsfuncties.
Lineaire-roterende motoren als bron van gegevens
Een ander voordeel van direct aangedreven lineaire-roterende motoren is dat ze 'automatisch' de parameters, het uitgeoefende koppel en de afgelegde afstand voor elke schroefsluiting registreren. Dat creëert optimale ondersteuning voor digitale transformatie, traceerbaarheid en kwaliteitsborging.
We hebben nu helemaal geen externe sensoren meer nodig.”
‘Onze machines maakten al gebruik van deze gegevens, maar nu hebben we helemaal geen externe sensoren meer nodig, zoals koppelopnemers of camerasystemen voor de hoogteregeling’, legt Markus Dierolf uit. Dit verlaagt de bekabelings- en materiaalkosten en vereenvoudigt de overdracht van gegevens naar overkoepelende systemen.
De nieuwe Optima-sluitunits worden zeer goed ontvangen door onze klanten. ‘De klant waar we onze eerste verpakkingslijn met LinMot-technologie plaatsten, heeft inmiddels al een tweede lijn besteld die een bestaand systeem gaat vervangen. Dat zegt mij genoeg.’
In de pijplijn: lineaire-roterende motoren in vulstations
Optima wil meer. Als volgende stap is het bedrijf van plan om ook vulstations uit te rusten met lineaire-roterende motoren, zo meldt Andreas Seitz: ‘De ontwerpen liggen er al. De argumenten zijn dezelfde als voor de sluitunits - maar hier hebben we bij elk vulpunt te maken met individuele, parametergebaseerde besturing van de vulnaaldbeweging. Daarmee willen we optimale vulresultaten leveren, ook voor extreem gevoelige producten die gemakkelijk kunnen ontbinden of die snel schuimen.’
Uitgebreide vultesten met de nieuwe technologie hebben al aangetoond dat dit mogelijk is. Op langere termijn wil de verpakkingsmachinespecialist de nieuwe vul- en sluittechniek uitbreiden naar andere bedrijfstakken en toepassingen.
LinMot heeft hier nog huiswerk te doen, en Seitz overlegt daartoe met de betrokken partijen: ‘Net zoals bij de bestaande explosieveilige lineaire motoren van LinMot, zouden wij hun lineaire-roterende aandrijvingen en servomotoren ook in ATEX-omgevingen willen kunnen gebruiken. En het zou erg handig zijn als de motoren en de besturingselektronica zich in één behuizing bevinden.’ LinMot is tegemoetgekomen aan deze wens en presenteerde de eerste oplossingen al op de beurs SPS/IPC/DRIVES 2017.
Dit artikel is gesponsord door Groneman